Nueve segundos es lo que tardó el ganador de ZEGA Evo Challenge en desmontar un par de maletas nuevas de la moto y volverlas a colocar. Esto lo consiguió en un evento organizado por Touratech USA, Rally Touratech 2019, para demostrar lo fácil y rápido que se puede manejar la nueva ZEGA Evo.
El dato puede no parecer importante cuando estás en la carretera pero sí que representa un punto de inflexión en la construcción de maletas de aluminio para motocicletas. Esto se debe a que el nuevo mecanismo de montaje es el primero en combinar la comodidad del sistema de Quickmount con la robustez necesaria para desplazamientos prolongados fuera de la carretera. Además, se han mejorado numerosos aspectos de la propia maleta.
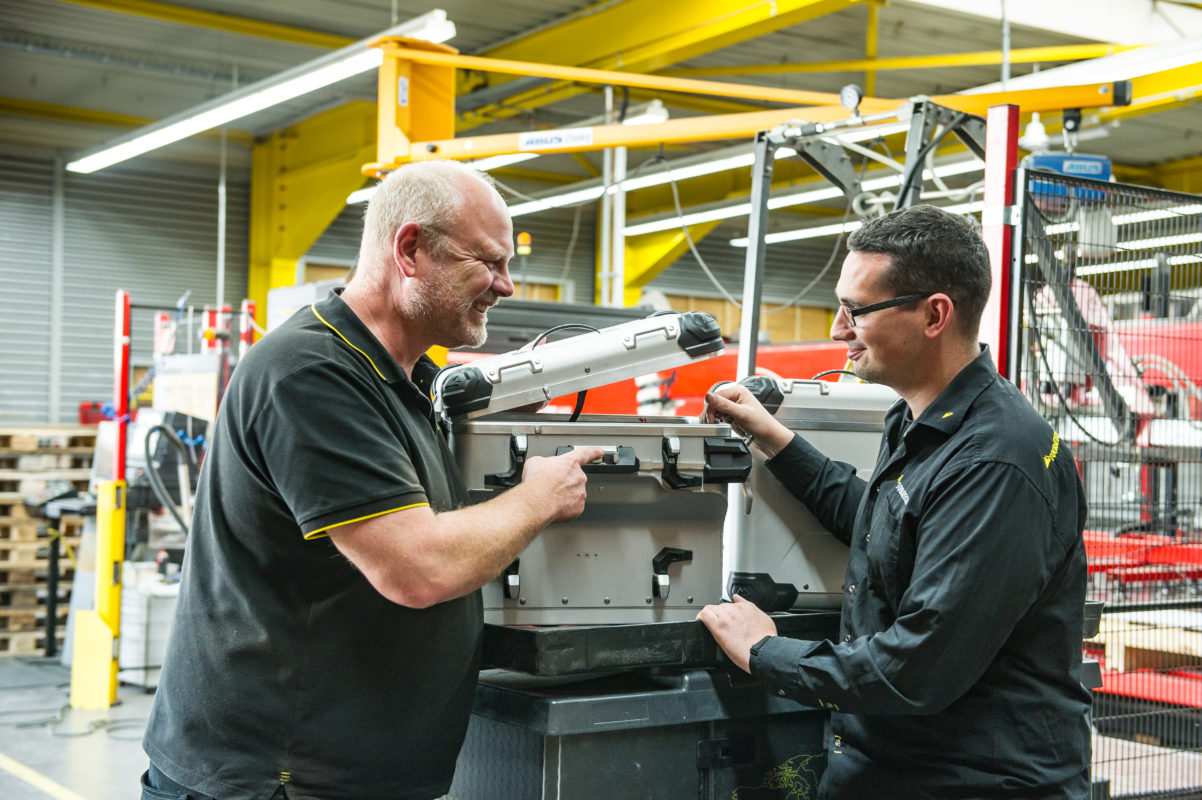
«En la ZEGA Evo, hemos centrado todos los conocimientos que hemos adquirido en estos 30 años de construcción de maletas de aluminio además de testearlas bajo condiciones extremas en innumerables ocasiones. Solo gracias a esta experiencia única es posible fabricar a gran escala un producto que requiere y exige tanta precisión y exactitud» afirmaba Jochen Schanz, Director de Operaciones y responsable de los nuevos desarrollos de Touratech.
Innovación tecnológica
Junto con los conocimientos técnicos de los desarrolladores, el segundo pilar importante para el éxito duradero de los productos de Touratech es el desarrollo permanente de la maquinaria. Las máquinas de alta tecnología que utiliza Touratech para la producción de ZEGA Evo son lo último en tecnología.

Incluso la manipulación de la materia prima esta totalmente automatizada. Esto tiene menos que ver con el ahorro de personal y más con garantizar un transporte cuidadoso de las hojas para evitar posibles arañazos. La prevención de daños caracteriza todo el proceso de producción de las maletas de aluminio. Las chapas decorativas tienen que pasar por innumerables etapas de trabajo: corte, medida, embutición de las tapas y las bases,… procurando que no sufran ningún daño.
Proceso de fabricación automatizado
Las maletas de aluminio son cortadas, exclusivamente, con láser. Esto se aplica a la chapa metálica de la carcasa exterior, donde los láseres planos de última generación garantizan diseños exteriores y patrones de agujeros precisos, así como a las bases y tapas dibujadas, que se recortan con precisión con un laser 3D después del moldeado.
Al igual que los pasos para el procesamiento de las piezas conformadas se agrupan en una célula mecanizada interconectada y totalmente automatizada, los pasos más importantes para la fabricación de la carcasa de la maleta también se procesan en un centro de mecanizado totalmente automatizado. En esta «célula de procesamiento de la carcasa exterior» primero se dobla la chapa, luego se estampa y por último, se suelda la unión por un robot.
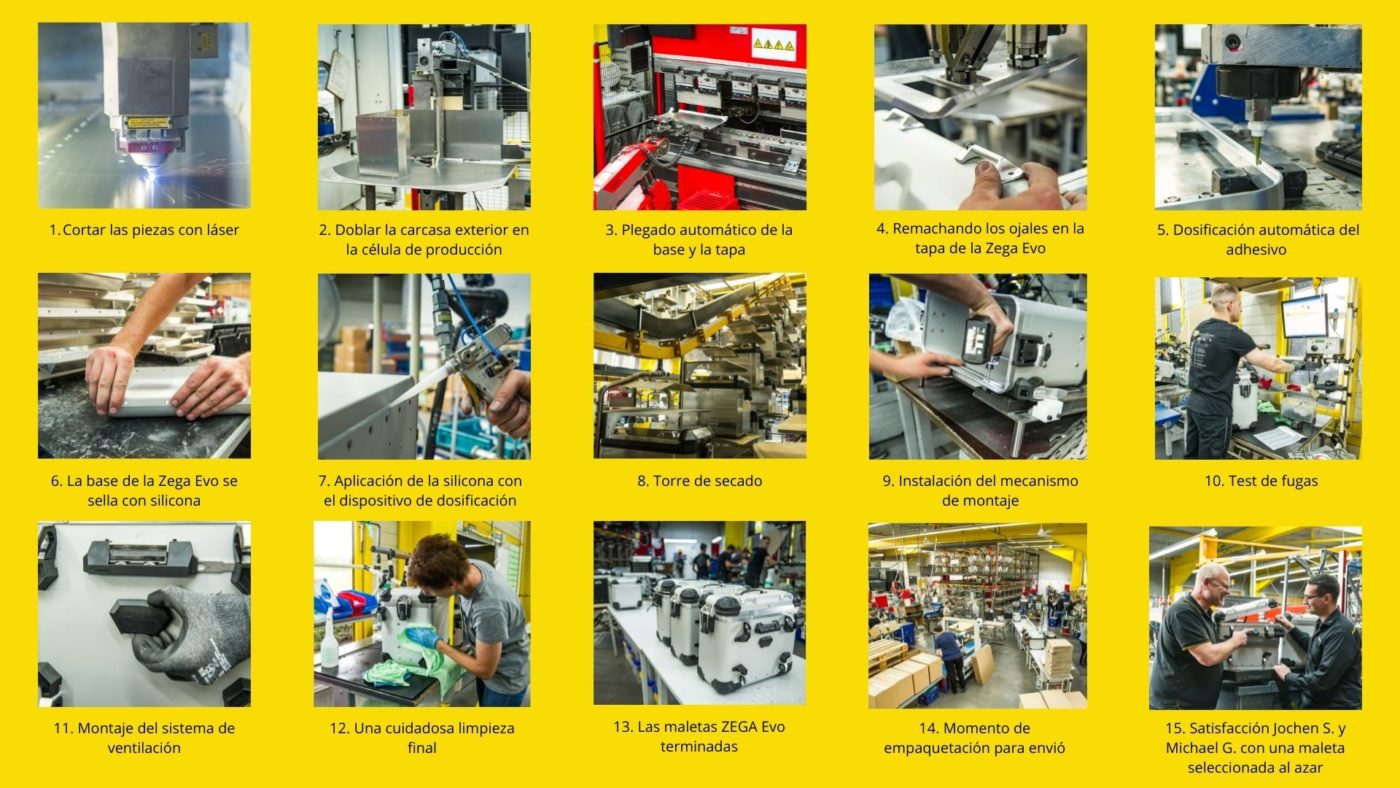
«Se ha dedicado una gran cantidad de recursos internos a la célula de procesamiento de la cáscara exterior. Ambos, el dispositivo para el curvado horizontal y la maquina de soldadura lineal para la unión precisa de la capa de aluminio tuvieron que ser especialmente diseñadas para la producción de maletas» nos comentaba Jochen Schanz.
Grado de cualificación del personal
A pesar del elevado grado de automatización, un gran número de empleados cualificados son requeridos para la producción de maletas. «Para empezar, esta el funcionamiento y la supervisión de nuestros centros de mecanizado. Después, esta el montaje de los componentes individuales. Aquí es donde se requiere la máxima precisión» , explicaba el jefe de producción para el montaje de maletas, Michael Gnädig.
La alta exigencia sobre la exactitud durante el montaje son el resultado del sofisticado diseño de las maletas, las cuales tienen una base semiflotante.
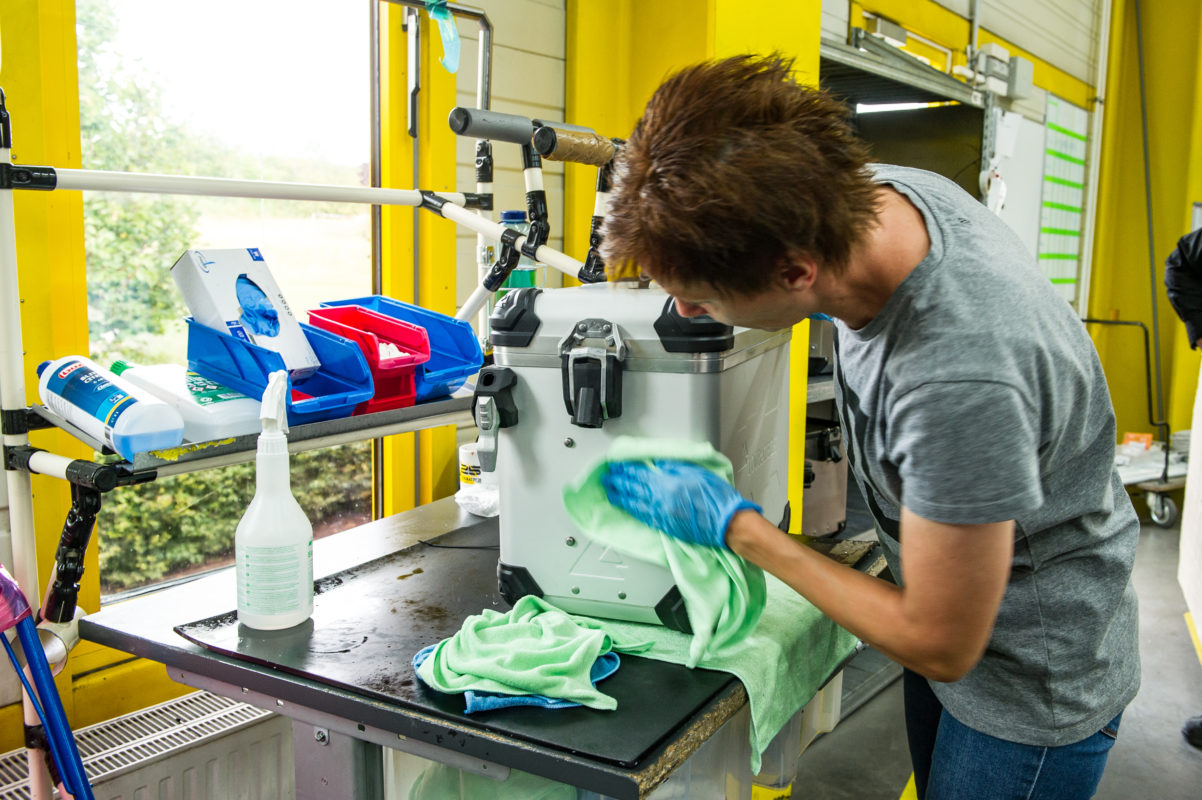
Cliff Vizer, coordinador de desarrollo de producto, añadía el siguiente ejemplo: «Este diseño, unido con remaches especiales, proporciona una extraordinaria rigidez a la vez que minimiza los problemas de grietas» . También se requieren unas tolerancias mínimas en la interacción entre la maleta y el mecanismo de montaje, con el fin de garantizar un montaje estable y un funcionamiento impecable.
Otro reto para los empleados del departamento de montaje es la gran variedad que tiene Touratech de maletas de aluminio. Por lo que, deben de estar especialmente atentos en todo momento.
Calidad de los productos de Touratech
Para asegurarse de que nada va mal incluso teniendo a sus empleados intensamente formados, la producción de Touratech cuenta con un sistema de control de calidad. Los controles van desde la inspección visual permanente hasta la rigurosa prueba final. A cada maleta se le asigna un número de serie individual con el que pueden rastrear los distintos pasos sin interrupción, de modo que cualquier fuente de error se puede rectificar inmediatamente.
Los empleados cuentan con el apoyo de numerosas soluciones de alta tecnología. Por ejemplo, la silicona se inyecta en la proporción exacta en la que sea requerida mediante un dispositivo de dosificación. También esta automatizado el complejo proceso de secado para el compuesto. «La silicona necesita unos valores de temperatura y humedad muy precisos para cuajar de forma óptima. Esto lo conseguimos de forma fiable en nuestra torre de secado, por la que pasan las maletas en un tiempo de proceso específico y totalmente automatizado» aseguraba Michael Gnädig.
Treinta y dos empleados trabajan en dos turnos de trabajo en la producción actual de maletas, 130 compañeros si incluimos producción de los bastidores y accesorios.
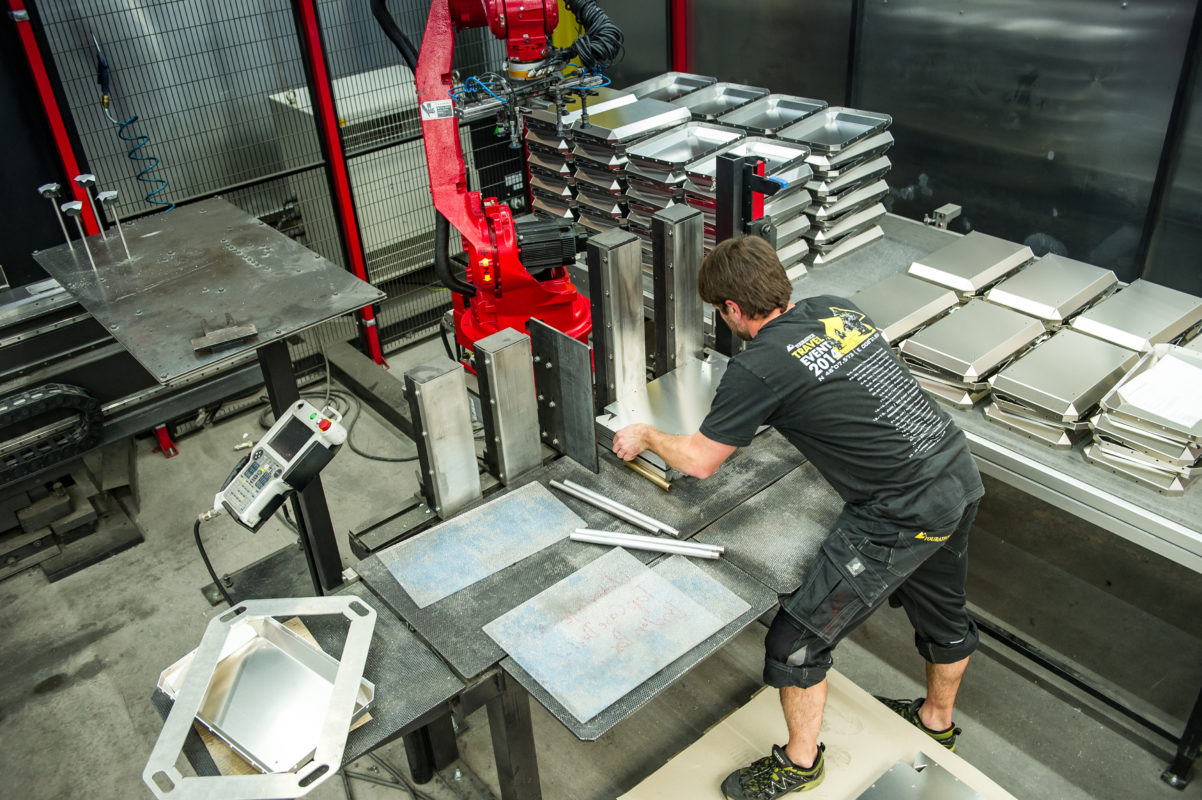
¿Es rentable en una Alemania con salarios elevados?
«Absolutamente» respondió Jochen Schanz «Existen muchas buenas razones por las que fabricar la ZEGA Evo en la localidad de Niedereschach. Aquí, tenemos distancias extremadamente cortas y esto, nos da grandes cantidades y elevados volúmenes de productos, reduciendo masivamente el coste de logística»
Michael continuo poniendo un ejemplo práctico «Aquí, en las instalaciones, con una producción diaria de hasta 400 maletas, manipulamos unos 60 contenedores de palés cada día, solo con componentes de la carcasa exterior. Esto equivale a dos o tres camiones articulados. Con este volumen que hay que manejar, la producción de componentes en el extranjero no es rentable económicamente»
A esto se añaden los requisitos de calidad. «Excepto por la obtención de la materia prima, por supuesto, y la fabricación de algunas piezas torneadas y de plástico, la fabricación de las maletas se realiza en su totalidad en la empresa. Esto nos da acceso a cada paso del proceso, lo que nos permite garantizar la máxima calidad posible» aseguraba Jochen Schanz.
Continuo hablando Cliff Vizer «Y tenemos un circuito de información muy estrecho, desde la producción hasta el desarrollo, lo que significa que podemos introducir mejoras a corto plazo, en el caso de que se produzcan dificultades en algunos pasos de la producción»
Maletas de viaje como «producto inagotable»
Treinta años después de que la maleta de ZEGA supusiera un gran avance en las maletas de aluminio para motos profesionales, la ZEGA Evo vuelve a marcar la diferencia en soluciones de transporte de alta calidad para motocicletas.

Pero, no solo los clientes de Touratech se benefician de la ventaja competitiva de la empresa, en lo que tiene que ver con el desarrollo y la producción de maletas de aluminio de alta calidad.
Numerosas empresas fabricadoras como por ejemplo BMW, Ducati o KTM tienen maletas fabricadas por Touratech para su propio gama de accesorios originales. Touratech produce, aproximadamente, un total de 100.000 maletas por año.
Y el viaje continua, no solo para los cientos de miles de usuarios de las maletas ZEGA en todo el mundo. Los desarrolladores tienen numerosas ideas para las futuras generaciones de maletas. «Para nosotros, el tema de las maletas de viaje está lejos de ser agotado» . Esto es todo lo que Jochen Schanz puede revelar por el momento.